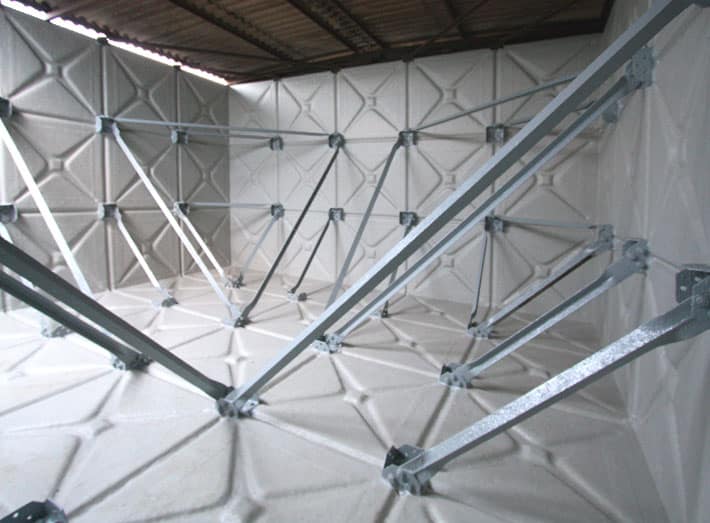
Sectional Tank Repair
One of James M Brown’s sectional tanks was in a poor state of repair, with several leaks due to corrosion. Tank repair experts Sui Generis were called in and recommended a complete fibreglass repair and lining. This saved the pigment company the cost of installing a new tank and left the sectional tank safe and secure for long-term use.
1. Completed tank repair with GRP lining to all walls, floors and struts.
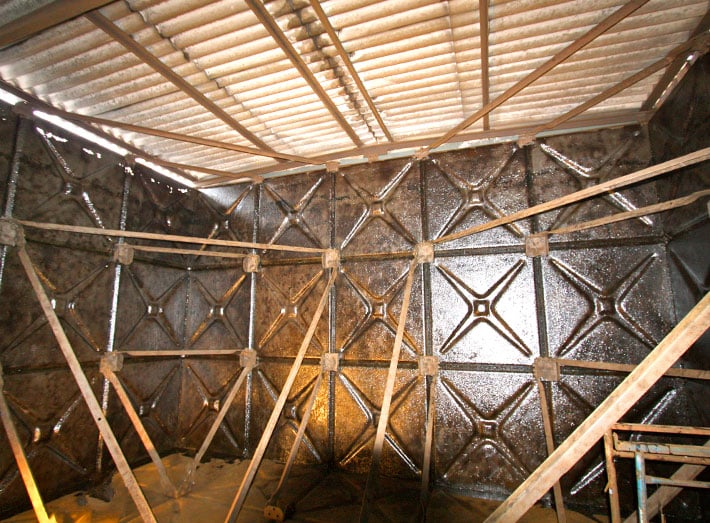
Off colour
Sui Generis were called in by the world’s largest manufacturer of cadmium pigments, James M Brown Ltd. The problem was an old storage tank that was suffering from corrosion and had started to leak. The UK company needed an economical way to repair the tank and repurpose it for a new function instead of taking on the significantly larger cost of replacing it.
After conducting a tank survey free of charge, Sui Generis recommended a complete repair and lining with GRP (fibreglass), which JMB were happy to accept.
2. Interior of the tank after grit blasting to remove rust and expose weaknesses, with resin primer to walls.
Harsh conditions
Normally a tank repair of this kind can be completed within a week, but the work coincided with a severe cold snap, with temperatures remaining below zero. In addition, the tank was elevated on stilts, which made it even colder. Nevertheless, the Sui Generis team was able to complete the whole refurbishment in only nine days.
The interior of the tank was first grit blasted to remove rust and reveal any weaknesses. Having positioned a tarpaulin outside to limit rain water coming in, work began on sealing the holes and reinforcing the areas of weakness with GRP. The whole tank was then given a watertight GRP lining to make it once more suitable for long-term use.
3. Sectional panels sealed with GRP.
FREE site survey
Call our specialist team to discuss your requirements, quote and get a FREE site survey: 01206 798 798
4. Completed: Tank repair and GRP lining to all walls, floors and struts.