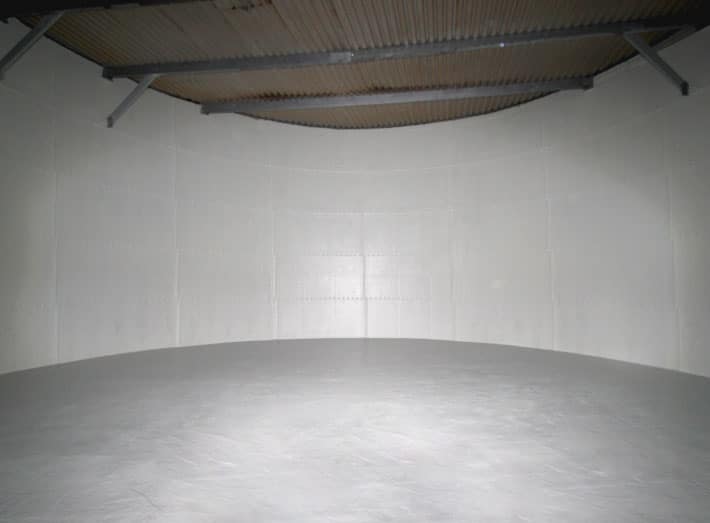
Lining Refurbishment
Having been called in to refurbish an industrial fire sprinkler tank suffering from corrosion, Sui Generis applied a corrosion and leak resistant FRP (composite) lining, extending the life of the tank by at least an extra 20 years.
Sui Generis applied a corrosion and leak resistant FRP lining, extending the life of the tank by at least an extra 20 years.
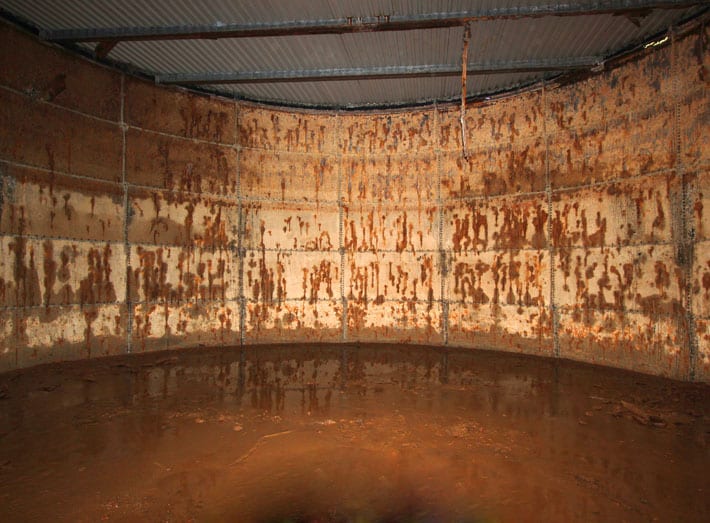
Corrosion
The client, producers of fine alcohol and distillers of spirits, took advantage of the free site survey offered by Sui Generis to assess an old 6m high x 11.6m diameter cylindrical sprinkler tank that was leaking and showing a significant degree of corrosion.
Tank within a tank
Sui Generis recommended a FRP lining system that effectively creates a new tank within the existing structure, as well as strengthening any weaknesses caused by the corrosion.
The tank also needed a low level manway hatch to be fitted, to reduce the risks from within the confined space. It made access much more manageable, providing easier entry for an access tower rather than lowering it through the roof top hatch.
Stable structure
Work started with pumping the residual water out from the tank, followed by grit blasting to all internal walls and floor surfaces to prepare the surfaces for the FRP lining. After fitting the manway hatch and removing the debris, the Sui Generis team applied the FRP lining to the whole of the interior.
A coat of polyester resin was applied, with internal FRP roof purlins installed followed by a final top coat. When cured, the FRP forms a stable structure with a high strength-to-weight ratio and good impact resistance.
The tank also needed a low level manway hatch to be fitted, to reduce the risks from within the confined space.
A bespoke manway was installed to facilitate safe and efficient access into the tank. This allowed for the setup of an internal access tower through the side opening, avoiding the need to lower equipment through a restricted rooftop hatch.
All internal wall joints were reinforced with high-quality fibreglass (FRP) matting. These were then carefully impregnated with polyester resin to create a strong, chemical-resistant bond and ensure long-term durability.
Before applying the main layers of FRP, a resin primer wash was used to encapsulate and seal the surface. This critical step enhances adhesion and ensures full bonding of the lining system to the substrate.
All Sui Generis personnel undergo comprehensive health and safety training. This includes certification for working at height and in confined spaces, ensuring that all site work is carried out to the highest professional and safety standards.
The FRP lining was completed with a seamless polyester resin coat. The bespoke manway access was integrated into the lining, providing a long-term solution for safe entry during future inspections and maintenance.
To complete the lining system, a final top coat was applied. This provides an additional layer of chemical resistance, enhances durability, and delivers a smooth, easy-to-clean surface finish.
The finished polyester resin-coated FRP lining also included the installation of GRP internal roof purlins. These components add structural support and are fully encapsulated within the corrosion-resistant lining system.
The entire internal tank surface was successfully lined and sealed with FRP and finished with a top coat. This provides a long-lasting, low-maintenance protective barrier against corrosion, abrasion, and chemical exposure.
Following the completion of the tank lining, the manway was securely sealed. It remains accessible for future maintenance and cleaning work, offering a safe and reusable entry point without compromising the integrity of the lining.